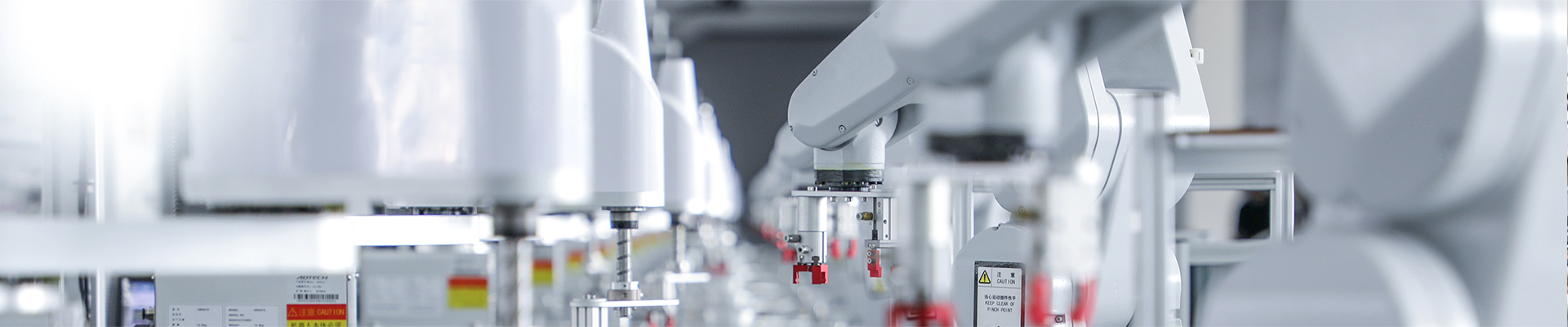
What is the Maximum Allowable Pulling Tension (MAPT) for underground cables, and how is it calculated and monitored during the pulling process?
2025-07-19The Maximum Allowable Pulling Tension (MAPT) is a critical parameter in underground cable pulling, representing the maximum force that can be safely applied to a cable during installation without causing damage to its conductors, insulation, or jacket. Exceeding MAPT can lead to costly cable failure, reduced lifespan, and project delays.
I. Calculation of MAPT:
MAPT is primarily determined by the cable manufacturer and depends on several factors:
-
Conductor Material: Copper conductors typically have a higher tensile strength than aluminum conductors.
-
Conductor Size (kcmil/mm²): Larger conductors can withstand greater pulling forces.
-
Conductor Type: Solid, stranded, or compacted conductors have different tensile properties.
-
Cable Design: The presence of a central strength member (especially in fiber optic cables), armor, or specific jacket materials can influence MAPT.
The general formula for calculating MAPT for power cables is often based on the allowable stress on the conductor:
-
For Copper Conductors: MAPT (lbs) ≤ Conductor kcmil ×8 lbs/kcmil
-
For Aluminum Conductors: MAPT (lbs) ≤ Conductor kcmil ×6 lbs/kcmil
For multi-conductor cables, the MAPT is usually based on the sum of the MAPT of all individual conductors, assuming they are sharing the load equally. However, for practical pulls, derating factors (e.g., 75-80%) are often applied to provide a safety margin, especially for multi-conductor pulls.
For fiber optic cables, the MAPT is often much lower and is specifically tied to the tensile strength of the aramid yarns or central strength member, not the delicate optical fibers themselves. Manufacturers provide explicit MAPT values for their fiber optic cables.
II. Monitoring MAPT During Pulling:
Precise monitoring of pulling tension is paramount to stay within the MAPT and prevent cable damage.
-
1. Automated Hydraulic Pullers with Load Cells: Our state-of-the-art hydraulic cable pullers are equipped with integrated digital load cells (dynamometers) that provide real-time tension readouts. This is the most accurate and reliable method.
-
2. Data Logging: Advanced pullers feature data logging capabilities that record pulling tension, speed, distance, and time throughout the entire pull. This data can be downloaded and analyzed post-pull, serving as an "as-built" quality assurance record and for troubleshooting.
-
3. Pre-Set Tension Limits: Our intelligent pullers allow operators to pre-set the MAPT. If the pulling tension approaches or exceeds this pre-set limit, the machine will automatically slow down or stop, preventing overstressing of the cable.
-
4. Continuous Communication: Maintaining clear and continuous communication between the pulling end, the feeding end, and intermediate points ensures that any anomalies (e.g., snags, increased friction) are immediately addressed.
-
5. Pulling Software & Calculations: Prior to any pull, specialized software is used to calculate theoretical pulling tensions based on cable weight, duct configuration (lengths, bends), and estimated coefficients of friction. This calculation helps determine appropriate equipment sizing and potential points of high stress.
By utilizing our precision-engineered pulling equipment with advanced monitoring capabilities, you can ensure that your underground cable installations are performed safely, efficiently, and without compromising the integrity of your valuable cable assets.